The term ‘Inventory’ refers to the stock of raw materials, spare parts and finished products held by a business firm. It is the aggregate quality of materials, resources and goods that are idle at a given point of time.
Inventory management refers to the process of managing the stocks of finished products, semi-finished products and raw materials by a firm. Inventory management, if done properly, can bring down cost and increase the revenue of a firm.
The inventory management process begins as soon as the firm has started production and ordered raw materials, semi-finished products or any other thing from a supplier. Once orders have been placed, there is generally a short period of time available to the firm to put an inventory management plan in place before the supplies are delivered.
Inventory management helps the firm to decide in advance where these supplies should be stored. If the firm is getting supplies of small- sized goods, it may not be much of a problem to store them, but in the case of large goods, one has to be careful so that the warehousing space is optimally utilised.
Contents
- Introduction to Inventory Management
- Meaning and Definition of Inventory
- Meaning of Inventory Management
- Objectives of Inventory Management
- Purpose of Inventory Management
- Importance of Inventory
- Importance of Inventory Management
- Classification of Inventories
- Types of Inventory
- Norms of Inventory
- Motives for Holding Inventory
- Costs of Holding Inventories
- Factors Influencing Inventory Management
- Economic Order Quantity
- Role of Financial Manager In Inventory Management
- Techniques of Inventory Management
- Benefits of Inventory Management
- Significant Problems of Inventory Management
What is Inventory Management: Introduction, Meaning, Definition, Objectives, Purpose, Importance, Classification, Types, Techniques, ABC Analysis, Norms, Motives, Factors and More…
Inventory Management – Introduction
A large part of total assets of a business is found in the form of inventory. To observe that the investment in inventory is not unnecessarily high, management should keep proper control on the amount and structure of inventory.
Because among all the current assets of business, inventory is the least liquid, any wrong in the management of inventory cannot be corrected easily and it can be very costly for the firm. Funds of the firm which are procured from internal as well as external sources need to be managed inventory and for this purpose inventory should be aware of all the factors affecting the level of management and the methods to control it.
The main objective of inventory management is to determine the level for each type of inventory. For this purpose the purchasing and carrying costs should be compared with their benefits. For example- when a firm purchases in bulk quantity, it’s out of stock costs and risk decreases but in case it continues to purchase, it reaches a point where it’s carrying costs exceed its benefits.
Therefore, the management should maintain only a proper level of inventory. Not only the financial manager is concerned with inventory management, but it also affects marketing and production managers. For determining an optimum level of inventory, proper coordination among all of them is essential.
Inventory is a current asset. Inventory means the goods which are kept for sale during the general operation of business. In case of trading institution it includes only finished goods.
In manufacturing concerns inventory may include:
(i) Inventory of Raw Material
(ii) Inventory of Work-in-Progress
(iii) Inventory of Finished Goods
(iv) Stores and Supplies.
In raw material, such goods are included which are converted into finished goods with the help of the production process. It is an important constituent of the cost of finished products. In the semi-finished goods all those goods are included which are in different stages of production processes and some process is to be employed to convert it into finished product.
After the completion of the manufacturing process, semi- finished goods are converted into finished products. Thus, finished goods are those goods on which the manufacturing work is complete and available for sale. Stores and supplies include fuel, coal, cotton, lubricant oil, broom, chemicals, etc.
The stores do not enter into the production process directly but are needed to run the production process smoothly and constitute an average small part in the total investment. Raw material and semi-finished goods help in the process of production and finished goods inventory helps in fulfilling the demand of customers.
The quantity of each type of inventory is different depending on the nature of different businesses.
For example- in a firm engaged in manufacturing activity, the level of all types of inventory will be high. But in a trading business, like wholesale or retail trade, the stock of finished products will be high but there will be no stock of work-in-progress, raw material and stores and supplies.
Inventory can be financed out of short term loans from banks but it will affect interest charges. Cost of inventory and interest charges can be reduced by proper inventory planning and control.
Inventory Management – Meaning and Definition of Inventory
The term ‘Inventory’ refers to the stock of raw materials, spare parts and finished products held by a business firm. It is the aggregate quality of materials, resources and goods that are idle at a given point of time.
The resources may be of any type; for example men, materials, machines or money when the resources involved in materials or goods in any stage of completion, inventory referred to as stocks. Hence, inventory refers to the ‘stocks’ that a business firm keeps to meet its future requirement of production and sales.
In financial parlance, Inventory is defined as the sum of the value of raw materials, fuels and lubricants, spare parts, maintenance consumables; semi processed materials and finished goods stock at any given point of time.
Inventories are maintained basically for the operational smoothness which they can affect by uncoupling successive stages of production, whereas the monetary value of inventory serves as a guide to indicate the size of the investment made to achieve this operational convenience.
Inventory Management – Meaning
Inventory management refers to the process of managing the stocks of finished products, semi-finished products and raw materials by a firm. Inventory management, if done properly, can bring down cost and increase the revenue of a firm.
The inventory management process begins as soon as the firm has started production and ordered raw materials, semi-finished products or any other thing from a supplier. Once orders have been placed, there is generally a short period of time available to the firm to put an inventory management plan in place before the supplies are delivered.
Inventory management helps the firm to decide in advance where these supplies should be stored. If the firm is getting supplies of small- sized goods, it may not be much of a problem to store them, but in the case of large goods, one has to be careful so that the warehousing space is optimally utilised.
From invoices to purchase orders, the purchase manager has to do a lot of paperwork and documentation involved in inventory management. Although the purchase manager is personally responsible to take care of inventory of the firm, the finance manager has to play an active role in the management of inventory. He, in fact, is the decision maker in the whole process of inventory management.
Any firm would like to keep higher levels of inventory. This will enable the firm to be more flexible in supplying to the customers and will find ease in its production schedule. Most of the customers may require immediate delivery and higher inventories may help meeting their demands and hence there would be less and less chances of sales being disrupted.
But there is always a cost involved in the inventory. This cost, as mentioned earlier, includes the capital cost of the stock and the costs of storing and carrying etc. On the other hand, holding a lower level of stock than required may result in stock-outs.
The cost of stock-out may be sales loss or customer dissatisfaction. The stock-outs may also result in delays or hold ups in the production process.
Given the benefits of holding inventory and cost of stock-outs, the firm will be tempted to hold maximum possible inventory. But this is costly too, because the funds blocked in inventory always have an opportunity cost. So the firm has to avert both overstocking as well as under stocking and determine an optimum level of inventory in such a way as to get the best return thereof.
It must weigh the benefits of holding inventory against its opportunity cost. While determining the optimum level of inventory, the firm has to take necessary steps to reconcile the differing viewpoints of production manager, marketing manager and the finance manager.
No doubt, most of the decisions relating to inventory are taken by the purchase manager in consultation with the production manager. Still the finance manager should ensure that the inventory is properly controlled and he should stress the need for the consideration of financial implications of inventory management.
Thus the inventory management focuses on determining and maintaining an optimum level of inventory in the firm. The inventory management seeks to maximise the wealth of the shareholders by designing and implementing such policies which attempt to minimise the cost of procuring and maintaining the inventory.
Inventory Management – Objectives
Objectives of Inventory Management are:
Through the efficient management of inventory the wealth of owners will be maximised. To reduce the requirement of cash in business, inventory turnover should be maximised and management should save itself from the loss of production and sales, arising from its being out of stock.
On the one hand, management should maximise stock turnover so that investment in inventory could be minimised and on the other hand, it should keep adequate inventory to operate the production and sales activities efficiently.
The main objective of inventory management is to maintain inventory at an appropriate level so that it is neither excessive nor short of requirement.
Thus, management is faced with two conflicting objectives:
(i) To keep inventory at sufficiently high level to perform production and sales activities smoothly.
(ii) To minimise investment in inventory at minimum level to maximise profitability.
Both inadequate and excessive quantities of inventory are undesirable for business. These mutually conflicting objectives of inventory management can be explained in the form of costs associated with inventory and the profits accruing from it.
Low quantum of inventory reduces costs and high level of inventory saves business from being out of stock and helps in running the production and sales activities smoothly.
The objectives of inventory management can be explained in detail as under:
(i) To ensure that the supply of raw material and finished goods will remain continuous so that the production process is not halted and the demands of the customers are duly met.
(ii) To minimise the carrying costs of inventory.
(iii) To keep investment in inventory at the optimum level.
(iv) To reduce the losses of theft, obsolescence and wastage, etc.
(v) To make arrangements for the sale of slow moving items.
(vi) To minimise inventory ordering costs.
Top 5 Purpose of Inventory Management
Purpose of Inventory Management are as follows:
1. To meet expected demand of the market intermediaries and end users.
2. Take advantage of Price Increase and Quantity Discounts.
3. To allow flexibility in production scheduling.
4. To seek protection from variation in raw material delivery time.
5. Reduce Transit Cost and duration.
Inventory Management – Top 4 Importance of Inventory
Importance of Inventory are as follows:
1. For smooth running of business operations inventory is indispensable. The prime components of business operations are production and marketing. Inventory establishes a very important linkage between the two.It separates both production and marketing and sets up coordination between the two.
Thus, production operations continue without any marketing barrier and marketing becomes effective without any production barrier.
2. Operation of each business concern is greatly affected by market factors especially the changes in demand. At the same time, the changes caused by trade cycles also affect the life of the business. If the concern continues production and marketing in a systematic way, it cannot bear with these changes.
There is a need to keep some finished goods as inventory, so that reconciliation can be made in accordance with the changes in demand. In this way inventory provides a cushion against the losses arising out of changes in demand or cyclical changes.
3. Since inventory by setting coordination between production and marketing makes production and distribution more easy and constant, the stability in employment in the business concern becomes possible.
In the absence of inventory, sometimes production has to be curtailed and sometimes production has to be increased. In both the situations, employment-status would tend to fluctuate. Thus, inventory helps in making employment comparatively stable.
4. In most of the business concerns, inventory forms the largest component of working capital. Inventory as a component of working capital is helpful in earning the profit. It is the inventory through which some profits can be earned.
Rest components of working capital are in liquid form fetching very minimum or zero profit. It has been proved that inventory turnover affects the rate of return.
Importance of Inventory Management
Inventory management covers a large number of problems including fixation of minimum and maximum levels, determining the size of inventory to be carried, deciding about the issue, receipts and inspection procedures, determining the Economic Order Quantity, proper storage facilities, keeping check over obsolescence and ensuring control over movement of inventories.
The importance of the inventory management is summarised as follows:
i. Transaction Motive to Avoid Loss Related to the Gap between the Demand and Supply of Goods:
As and when the demand for the product arises, the firm has to deliver goods. The stock of RM and WIP is also needed for an efficient and smooth production run. If demand has to be met in time, the goods from the plant have to be supplied in time.
Thus adequate inventory of RM, WIP and FGs is needed to manufacture the product, allow smooth flow of material and the final product in the production process and distribution cycle of the firm to match the predicted demand and related supply of the product.
ii. Gaining Quantity Discounts:
The firm purchases and stores material during favourable economic conditions in order to minimise the cost of material input. Suppliers usually give trade discounts on bulk purchases by customers. Thus, the firm gains from discount on the bulk purchases of material inputs. This decreases the overall cost to the firm.
iii. Reduction in Ordering Cost:
The costs involved between the time of placing the order and receiving the supply of goods ordered which are then inspected and counted before final payment are known as operating cost. Operating costs are independent of the size of order.
Hence, if the firm increases the size of its order and thus decreases the frequency of its order, its Operating Cycle is reduced, reducing the overall cost to the firm.
iv. Efficiency and Economy of Production Run:
There are certain costs in starting the machine to run the production process. These costs are termed as start-up costs. Start-up cost is independent of the length (time duration) of production run.
Thus, if the firm increases its production run (i.e., for a longer time period) and thus decreases the frequency of production run, start-up costs are reduced, thereby reducing the overall cost to the firm. Such production runs are said to be efficient and profitable.
v. Precautionary Motive:
Inventory acts as buffer stock. It acts as a shock absorber and co-ordinates the various interdepartmental processes such as – purchasing, production and selling. Adequate inventory of RM and WIP is maintained to run large, efficient and smooth production runs.
vi. Creating Goodwill among Customers:
Meeting customers’ demand in time even in case of errors in forecasted demand creates goodwill and loyalty on part of the customers.
Inventory Management – Classification of Inventories: Raw Material, Component Parts, Work -in Process, Finished Good and Supplies
Classification of Inventories are as follows:
(a) Raw Material
A raw material inventory includes all items that, after being received at the plant, require additional processing before becoming an identifiable part of the finished product.
(b) Component Parts
This classification of inventory is applied to component parts of a product that need no additional processing before being assembled into the finished product. The TV picture tube that is the finished product of one manufacturer becomes a purchased part to the television set manufacturer.
(c) Work -in Process
Work-in-process is the inventory of material, the flow of which is controlled by production control procedures.
(d) Finished Good
This classification applied to the quantities of finished goods that are held at the factory awaiting shipment. In many instances, however, it will include stocks held in warehouses owned and operated by the manufacturer, or stock held on dealers’ floors on consignment.
(e) Supplies
All the materials needed for the operation of the plant that are not used as parts of the finished product are classified as supplies. The material that becomes part of the finished product is called “direct material”.
Inventory Management – Types of Inventory: Raw Materials, Work-In-Process and Finished Goods
Inventories consist of raw material, work-in-process and finished goods which are held by a firm in the ordinary course of business, either for sale or for the purpose of using them in the process of producing goods and services. Inventories constitute the most significant part of current assets for a majority of firms.
There are three types of inventories:
1. Raw materials,
2. Work-in-process and
3. Finished goods.
1. Raw Materials:
This type of inventory includes direct materials that are used in the manufacture of a product, or the components that are used to assemble a finished product. Raw materials may also include partially finished goods or materials.
For example, for an ice cream manufacturing firm, milk, sugar and preservatives are raw materials; while for a computer manufacturer, chips, circuit boards and transistors are raw materials. Inventory items may be classified as raw materials if the organization has purchased them from an outside firm, or if they are used to make components.
2. Work-In-Process:
This includes the partially completed goods, parts, or sub-assemblies that are not yet part of the finished product inventory and no longer form part of the raw materials inventory. Work-in-process inventory forms a part of the current assets of a firm and is valued usually at lower cost and realizable value by following the accounting principle of conservatism.
This is also known as work-in-progress that includes partly finished goods and materials, sub-assemblies, etc., which are held in between the stages of production; the stock of goods, which are partly processed and are still in the process of production; the partially assembled items; finished goods that have not yet been packaged and inspected, and also the raw materials that have moved from storage to a pre-assembly area.
For example, in an ice cream firm, the milk may come into a storage area, where they are raw material, but once they have been moved out of the storage area and onto the assembly line for making ice cream, they become work-in-process inventory.
If a business makes and sells chairs, work-in-process inventory would include any unfinished chairs. In a small firm, work-in-process goods may be stored in the same area as raw materials and finished goods.
3. Finished Goods:
Finished goods are all those items of products that are fit for sale and ready to be shipped out or sold directly to customers, including to wholesalers and retailers. Finished goods may be waiting in a storage area or on a shop floor.
If the amount of inventory of finished goods increases faster than the amount of raw goods and work-in-process goods, then production may need to slow down until more finished goods are sold. In some businesses, where goods are made to order, goods are not included in the finished goods inventory until they are sold.
In manufacturing concerns, there are usually three types of inventory as explained above. However, the only form of inventory, in case of retailers and distributors, are finished goods. For example, in a retail business that buys and sells toys, the unsold items of the toys constitute the inventory of finished goods.
For service concerns, inventory is any supply that is used up to provide the services. For instance, a beauty saloon’s inventory includes various cosmetics that are used during its service to the clients.
Apart from these, other types of inventory include maintenance, repair and operating items. These include all the items that an organization needs to operate, for example, office equipment, packing boxes and loose tools to repair equipment. There are also other types of inventory that are classified on the basis of the purpose they serve.
These include transit inventory, which are products or components that are being moved from one location to another, such as from a warehouse to a factory; buffer inventory, which are excess inventory items that are kept on hand to protect against supply problems.
Some of these problems are poor quality materials, slower delivery of raw materials and maintenance of anticipatory inventory, which are stocked to meet any excess demand.
For instance, during the festive season of Diwali, demand for consumer goods is quite high. Therefore, sellers maintain high inventory levels to meet the excess demand.
Inventory Management – Norms of Inventory
The norms are the limits for inventory could be set by either the top management, or the materials management department. The top management usually sets monetary limits for investment in inventories.
The materials department then has to allocate this investment to the various items and ensure the smooth operation of the company. It would be worthwhile if the inventory norms are set by the “management by objectives” concept.
In the setting up of the norms, the involvement of persons who are directly responsible for maintaining the inventories is very desirable. Other departments involved in setting the norms are finance, production, marketing and materials control.
The norms of inventory should be converted to specially spell out parameters like the number of stock outs permitted, the sales to inventory ratio and inventory to consumption ratio.
Inventory Management – Top 3 Principal Motives for Holding Inventory: Transaction Motive, Precautionary Motive and Speculative Motive
Like cash, there are three principal motives for holding inventory:
a) Transaction Motive:
It facilitates uninterrupted production & delivery of order at a given right time. This motive means holding inventory for satisfying sales and production requirements. Normally, every production process takes some time.
When the customers come for purchase, the firm needs ready goods so that it can deliver them to customers on time. If the firm does not have ready finished goods, and the customer needs goods immediately, the firm would not be able to supply on time.
Therefore some amount of finished goods must be kept ready so that sales are not lost. Similarly, in the production process, the factory may demand raw materials continuously. If the firm does not have ready stock of raw material, then it will order for purchase.
Till the raw materials arrive, it may have to stop its production process. Therefore, in order to keep the production process uninterrupted, raw materials stock has to be kept. The same logic can be applied on WIP inventory at different stages of the production process.
b) Precautionary Motive:
It is for unexpected changes in demand and supply factors. Inventory kept with precautionary motive is kept to act as a buffer if the actual level of activity (sales or production) exceeds the planned or anticipated levels.
Again, this motive is applicable to all types of inventory viz. raw material, work in process and finished goods. For example, a restaurant keeping extra supplies to meet extra demand on Saturday and Sundays.
c) Speculative Motive:
This motive means keeping large stocks in anticipation of change in prices that would enable the firm to take advantage of changes in prices and getting quantity discounts. This motive also works when the firm is anticipating a change in the product.
i. Inventory Holding-
Practical Considerations- These motives are the theoretical explanations for holding stock. But in reality, inventory serves the “decoupling” purpose. What is decoupling? It means making two processes independent of each other. For example, holding raw material inventory will decouple production and purchase functions.
If we do not hold any raw material inventory, what will happen? Then every time there is a requirement of raw material in the factory (production process), immediate purchase will be needed. The production process will “depend” on the purchase to run smoothly.
But by keeping raw material stock, we decouple the production and purchase process. The production runs smoothly even if purchase of materials is taking time. Need a policy for balanced investment in inventory including excessive (dangers), inadequate (dangers).
Similarly, WIP inventory acts to decouple various stages of the production process. One stage of the production process becomes independent of the previous stage if some WIP inventory is kept from the previous stage.
Likewise, the Finished goods inventory decouples selling & distribution from production. If finished goods are readily available in stock, the marketing team does not need to consult the production department before committing supply of an order.
Inventory Management – Costs of Holding Inventories
When a firm holds goods for future sale, it exposes itself to a number of risks and costs. The effective management of inventory involves a trade-off between having too little and too much inventory. In achieving this trade-off, the financial manager should realise that risks and costs may be closely related.
The costs of holding inventories are as follows:
1. Material Costs:
These are the costs of purchasing the goods plus transportation and handling. This may be calculated by adding the purchase price (less and discounts), the delivery charges and the sales tax (if any).
2. Order Costs:
These are the variable costs of placing an order for the goods. Each separate shipment involves certain expenses connected with requesting and receiving materials.
Examples of these costs are the typing of the order and the inspection of the goods after they arrive. The fewer the orders, the lower the order cost will be for the firm.
3. Carrying Costs:
These are the expenses of storing goods. Once the goods have been accepted, they become part of the firm’s inventories.
The following are the examples of different kinds of carrying costs:
i. Storage Costs
The firm must provide for storage space, usually through the operation of a warehouse or supply room. The firm must employ workers to move, clean, count, record and protect the goods. All of these activities dealing with the physical holding of the goods are considered storage costs.
ii. Insurance
In spite of the best precautions taken, firms must protect themselves against such hazards as fire or accidents in the warehouse. Larger amounts of inventory require larger amounts of insurance. The insurance premiums represent a carrying cost on inventory.
iii. Obsolescence and Spoilage
When firms hold goods, they expose themselves to the possibility that the goods will not be saleable when the time arrives. Obsolescence is the cost of being unable to sell goods because of current market factors deriving from changes in styles, tastes or other factors.
If a product is no longer wanted, the firm must sell it at a fraction of its value or destroy it. Spoilage occurs when a product is not saleable because of deterioration during the storage, such as – foods that rot, plants that die, garments that are attacked by moths, candles that discolour or chemicals that decompose.
iv. Damage or Theft
Although a firm makes every effort to protect goods against damage and safeguard items against pilferage, goods are damaged and stolen. A portion of these expenses are not covered by insurance and are losses to the firm. Some businesses, particularly retail stores and firms producing luxury goods, face this carrying cost.
4. Cost of Funds Tied up in Inventory:
Whenever a firm commits its resources to inventory, it is using funds that Otherwise might be available for other purposes. A portion of the inventory is financed by trade credit from suppliers and involves no cost.
The balance of the inventory must be financed from the firm’s general funds and involves a cost. If the firm is considering an expansion of inventory and plans to borrow to obtain funds, the firm will have to pay interest on the additional debt.
5. Cost of Running Out of Goods:
Whenever a firm incurs shortages of products, it incurs costs. If the firm is unable to fill an order, it risks losing a sale. If the firm runs out of raw materials, it may force a costly shutdown of the production process. Adequate inventory helps reduce additional costs and lost revenues due to shortages.
Factors Influencing Inventory Management
Factors Influencing Inventory Management are as follows:
Many factors influence inventory management and control. The principal effects of these factors are reflected most strongly in the levels of inventory and the degree of control planned in the inventory control system. The factors include type of product, type of manufacture, volume of output and others.
(a) Type of Product:
If the materials used in the manufacture of the product have a high unit value when purchased, a much closer control is usually in order. If the material used in the product is in short supply or is rationed by the government, this may influence the purchase of this material and stock maintained.
Material required to product made-to-order items needs strict control to ensure that no item is lost in the process of manufacture. Such materials are of special and expensive type and a loss of any small part will hold the production.
(b) Type of Manufacture:
Continuous manufacture is common to the manufacture of standard products. However, some standard products are made in batches. Where continuous manufacture is employed, the rate of production is the key factor.
Here inventory control is of major importance and in reality controls the production of the product. The economic advantage of this type of manufacture is the uninterrupted operation of the machines and assembly lines in the plant.
(c) Volume of Product:
The volume of product to be made, as represented by the rate of production, may have little effect on the complexity of the inventory problem. Literally millions of brass bases for light bulbs are manufactured, even money involving the control of only two principal items of raw materials inventory.
(d) Other Factors are:
- The potential savings that might be anticipated from improved control of inventories.
- The nature and size of inventories and their relationship to other functions in the company, such as manufacturing, finance, marketing etc.
- The objectives of the company as they relate to inventories and the level of service to be provided to customers.
- The current, or potential, availability of data that can be used in controlling inventories.
- The present method for controlling inventories and for making inventory decisions.
Inventory Management – Economic Order Quantity (With Assumptions)
Stocks are held to satisfy demands quickly to allow unimpeded production, to take advantage of bulk purchasing, as a necessary part of the production process, and to absorb seasonal and other fluctuations.
However, stocks accumulate unnecessarily through poor control methods, obsolescence, poor liaison and sub-optimal decision making. One basic inventory control system is called the re-order level under which the usual replenishment order quantity is the EOQ (economic order quantity).
This ordering quantity minimizes the balance of cost between inventory holding costs and re-order costs. The prime objective of inventory management is to find out and maintain optimum level of investment in inventory to minimize the total costs associated with it.
The EOQ is the optimum size of the order for a particular item of inventory calculated at a point where the total inventory costs are at a minimum for that particular stock item.
It is an optimum size of either a normal outside purchase order or an internal production order that minimizes total annual holding and ordering costs of inventory. Stock-out costs are difficult to incorporate into this model.
Since they are based on qualitative and subjective judgment. The ordering costs are the costs of placing a separate order multiplied by the number of separate orders placed in the period.
The carrying costs can be calculated based on the assumption that the annual cost of carrying a particular stock item on average, half the stock is on hand all the time in addition to the safety or buffer stock.
The fewer the orders, the lower costs of ordering, but the greater the size of the order the greater the costs of carrying. The safety or buffer stock has no bearing on the EOQ, only on the timing of orders.
Assumptions of EOQ:
To be able to calculate a basic EOQ certain assumptions are necessary:
a. That there is a known, constant stock holding cost.
b. That there is a known, constant ordering cost.
c. That rates of demand are known and constant.
d. That there is a known, constant price per unit, i.e., there are no price discounts.
e. That replenishment is made instantaneously, i.e., the whole batch delivered at once.
Role of Financial Manager In Inventory Management – Inventory Turnover Ratio and Ageing Schedule of Inventory
In the preceding section, the costs and benefits associated with inventories have been discussed. The financial manager shall be aware of advantages and disadvantages associated with high level and low level of inventories.
The financial manager can arrive at the optimum quantity of inventories to be ordered by using the EOQ model. The model helps in determining the optimum size of the order but another issue relating to time for placing the order is sorted out by evaluating reorder level.
The financial manager on the basis of his past experience can estimate the time usually taken by suppliers to deliver the inventories after placement of an order i.e., lead time. Thus, using lead time and safety stock, reorder level can be ascertained.
Besides the evaluation of order size of inventories and timing for placing order for inventories, the financial manager shall take care of maintaining inventories for which ABC system/analysis criteria may be used in addition to these techniques, the financial manager shall use inventory turnover ratio and ageing schedule of inventory which are briefly discussed below:
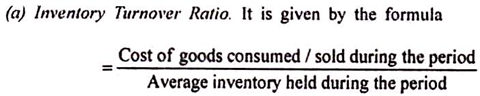
The ratio helps in determining the amount of investment to be made in various kinds of inventories being maintained by the firm.
On the basis of ratio, inventories are classified into four types:
(i) Slow moving inventories
(ii) Fast moving inventories
(iii) Dormant inventories
(iv) Obsolete inventories.
The firm makes more investment in fast moving inventories and pays less attention to slow moving inventories. Dormant inventories are those inventories which have no demand and they are to be returned back to the suppliers or disposed of in the market at salvage value. Sometimes, they may be retained if the financial manager expects their demand in future.
(b) Ageing Schedule of Inventory
The financial manager shall determine the time lag between the date of purchase of inventories and the date of their usage for production purpose. This will help in identifying the rate at which various inventories are consumed.
Using this information, the inventory manager will be able to take adequate steps while purchasing inventories so that inventories do not get deteriorated before they are consumed for the production process.
Techniques of Inventory Management
Some of the most important techniques of inventory Management are discussed below:
Technique # 1. Setting Up of Various Stock Levels:
To avoid over-stocking and understocking of materials, the management has to decide about the maximum level, minimum level, re-order level, danger level and average level of materials to be kept in the store.
These terms are explained below:
(i) Re-Ordering Level:
It is also known as – ‘ordering level’ or ‘ordering point’ or ‘ordering limit’. It is a point at which order for supply of material should be made. This level is fixed somewhere between the maximum level and the minimum level in such a way that the quantity of materials represented by the difference between the re-ordering level and the minimum level will be sufficient to meet the demands of production till such time as the materials are replenished.
Reorder level depends mainly on the maximum rate of consumption and order lead time. When this level is reached, the store keeper will initiate the purchase requisition.
Reordering level is calculated with the following formula:
Re-order level = Maximum rate of consumption x maximum lead time
(ii) Maximum Level:
Maximum level is the level above which stock should never reach. It is also known as ‘maximum limit’ or ‘maximum stock’. The function of maximum level is essential to avoid unnecessary blocking up of capital in inventories, losses on account of deterioration and obsolescence of materials, extra overheads and temptation to thefts etc.
This level can be determined with the following formula:
Maximum Stock level = Reordering level + Reordering quantity – (Minimum Consumption x Minimum re-ordering period)
(iii) Minimum Level:
It represents the lowest quantity of a particular material below which stock should not be allowed to fall. This level must be maintained at every time so that production is not held up due to shortage of any material. It is that level of inventories of which a fresh order must be placed to replenish the stock.
This level is usually determined through the following formula:
Minimum Level = Re-ordering level – (Normal rate of consumption x Normal delivery period)
(iv) Average Stock Level:
Average stock level is determined by averaging the minimum and maximum level of stock.
The formula for determination of the level is as follows:
Average level =1/2 (Minimum stock level + Maximum stock level)
This may also be expressed by Minimum level + 1/2 of Re-ordering Quantity.
(v) Danger Level:
Danger level is that level below which the stock should under no circumstances be allowed to fall. Danger level is slightly below the minimum level and therefore the purchases manager should make special efforts to acquire required materials and stores.
This level can be calculated with the help of following formula:
Danger Level = Average rate of consumption x Emergency supply time.
(vi) Economic Order Quantity (E.O.Q.):
One of the most important problems faced by the purchasing department is how much to order at a time. Purchasing in large quantities involves lesser purchasing cost. But the cost of carrying them tends to be higher. Likewise if purchases are made in smaller quantities, holding costs are lower while purchasing costs tend to be higher.
Hence, the most economic buying quantity or the optimum quantity should be determined by the purchase department by considering the factors such as cost of ordering, holding or carrying.
This can be calculated by the following formula:
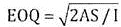
Where A stands for annual requirements of an item in terms of rupees;
S stands for cost of placement of an order in rupees; and
I stand for inventory carrying cost per unit per year in rupees.

Storage (holding) cost per unit = cost per unit x Storage cost (%)
Technique # 2. Preparation of Inventory Budgets:
Organizations having huge material requirements normally prepare purchase budgets. The purchase budget should be prepared well in advance. The budget for production and consumable material and for capital and maintenance material should be separately prepared.
Sales budgets generally provide the basis for preparation of production plans. Therefore, the first step in the preparation of a purchase budget is the establishment of a sales budget.
As per the production plan, material schedule is prepared depending upon the amount and return contained in the plan. To determine the net quantities to be procured, necessary adjustments for the stock already held is to be made.
They are valued at standard rate or current market price. In this way, the material procurement budget is prepared. The budget so prepared should be communicated to all departments concerned so that the actual purchase commitments can be regulated as per budgets.
At periodic intervals actuals are compared with the budgeted figures and reported to management which provides a suitable basis for controlling the purchase of materials.
Technique # 3. Maintaining Perpetual Inventory System:
This is another technique to exercise control over inventory. It is also known as an automatic inventory system. The basic objective of this system is to make available details about the quantity and value of stock of each item at all times. Thus, this system provides a rigid control over stock of materials as physical stock can be regularly verified with the stock records kept in the stores and the cost office.
Technique # 4. Perpetual Inventory Control System:
In a large business it is essential to have information about continuous availability of different types of materials and stores purchased, issued and their balance in hand. The perpetual inventory control system enables the manufacturer to know about the availability of these materials and stores without undergoing the cumbersome process of physical stock taking.
Under this method, proper information relating to receipt, issue and materials in hand is kept. The main objective of this system is to have accurate information about the stock level of every item at any time.
Perpetual inventory control system cannot-be successful unless and until it is accompanied by a system of continuous stock taking i.e., checking the total stock of the concern 3 or 4 times a year by picking 10 or 15 items daily (as against physical stock taking which takes place once a year).
The items are taken in rotation. In order to have more effective control, the process of continuous stock taking is usually undertaken by a person other than the storekeeper. This will check the functioning of the storekeeper also.
The items may be selected at random to have a surprise check. The success of the system of perpetual inventory control depends upon the proper implementation of the system of continuous stock taking.
Technique # 5. Establishing Proper Purchase Procedures:
A proper purchase procedure has to be established and adopted to ensure necessary inventory control.
The following steps are involved:
(i) Purchase Requisition
It is the requisition made by the various departmental heads or storekeepers for their various material requirements. The initiation of purchase begins with the receipts of a purchase requisition by the purchase department.
(ii) Inviting Quotations
The purchase department will invite quotations for supply of goods on the receipt of purchase requisition.
(iii) Schedule of Quotations
The schedule of quotations will be prepared by the purchase department on the basis of quotations received.
(iv) Approving the supplier
The schedule of quotations is put before the purchase committee who selects the supplier by considering factors like price, quality of materials, terms of payment, delivery schedule etc.
(v) Purchase Order
It is the last step and the purchase order is prepared by the purchase department. It is a written authorisation to the supplier to supply a specified quality and quantity of material at the specified time and place mentioned at the stipulated terms.
Technique # 6. Inventory Turnover Ratio:
These are calculated to minimise the inventory by the use of the following formula – Inventory Turnover Ratio= Cost of goods consumed or sold during the period/ Average inventory held during the period.
The ratio indicates how quickly the inventory is used for production. Higher the ratio, shorter will be the duration of inventory at the factory. It is the index of efficiency of material management.
The comparison of various inventory turnover ratios at different items with those of previous years may reveal the following four types of inventories:
(i) Slow moving Inventories
These inventories have a very low turnover ratio. Management should take all possible steps to keep such inventories at the lowest levels.
(ii) Dormant Inventories
These inventories have no demand. The finance manager has to make a decision whether such inventories should be retained or scrapped based upon the current market price, conditions etc.
(iii) Obsolete Inventories
These inventories are no longer in demand due to their becoming out of demand. Such inventories should be immediately scrapped.
(iv) Fast moving inventories
These inventories are in hot demand. Proper and special care should be taken in respect of these inventories so that the manufacturing process does not suffer due to shortage of such inventories.
Technique # 7. Abc Analysis:
In order to exercise effective control over materials, A.B.C. (Always Better Control) method is of immense use. Under this method materials are classified into three categories in accordance with their respective values.
Group ‘A’ constitutes costly items which may be only 10 to 20% of the total number of items but account for about 50% of the total value of the stores. A greater degree of control is exercised to preserve these items.
Group ‘B’ consists of items which constitutes 20 to 30% of the store items and represent about 30% of the total value of stores. A reasonable degree of care may be taken in order to control these items.
In the last category i.e., Group ‘C’ about 70 to 80% of the items are covered costing about 20% of the total value. This can be referred to as the residuary category. A routine type of care may be taken in the case of third category.
This method is also known as ‘stock control according to value method’, ‘selective value approach’ and ‘proportional parts value approach’. If this method is applied with care, it ensures considerable reduction in the storage expenses and it is also greatly helpful in preserving costly items.
Technique # 8. Just in Time:
The Just in Time (JIT) method works to lessen the volume of inventory that a business has on hand. It is considered a risky technique because you only purchase inventory a few days before it is needed for distribution, sale or production so that the items arrive just in time for use.
JIT helps organisations save on inventory holding costs by keeping stock levels low, and eliminates situations where deadstock sit on shelves for months on end. One needs to conduct thorough research into customer buying habits, seasonal demand, and source for reliable suppliers and channels of transportation before implementing JIT into a business operations to minimise risks and screw ups.
Advantages:
Just-in-Time Systems:
Following are the advantages of adopting Just-in-Time Manufacturing Systems:
i. Just-in-time manufacturing keeps stock holding costs to a bare minimum. The release of storage space results in better utilization of space and thereby bears a favourable impact on the rent paid and on any insurance premiums that would otherwise need to be paid.
ii. Just-in-time manufacturing eliminates waste, as out-of-date or expired products; do not enter into this equation at all.
iii. As under this technique, only essential stocks are obtained, less working capital is required to finance procurement. Here, a minimum re-order level is set, and once that mark is reached, fresh stocks are ordered making this a boon to inventory management too.
iv. Due to the aforementioned low level of stocks held, the organization’s return on investment (referred to as ROI, in management parlance) would generally be high.
v. As just-in-time production works on a demand-pull basis, all goods made would be sold, and thus it incorporates changes in demand with surprising ease. This makes it especially appealing today, where the market demand is volatile and somewhat unpredictable.
vi. Just-in-time manufacturing encourages the ‘right first time’ concept, so that inspection costs and cost of rework is minimized.
vii. High quality products and greater efficiency can be derived from following a just-in-time production system.
viii. Close relationships are fostered along the production chain under a just-in-time manufacturing system.
ix. Constant communication with the customer results in high customer satisfaction.
x. Overproduction is eliminated when just-in-time manufacturing is adopted.
Disadvantages:
Just in Time Technique:
Following are the disadvantages of Adopting Just-In-Time Manufacturing Systems:
i. Just-in-time manufacturing provides zero tolerance for mistakes, as it makes re-working very difficult in practice, as inventory is kept to a bare minimum.
ii. There is a high reliance on suppliers, whose performance is generally outside the purview of the manufacturer.
iii. Due to there being no buffers for delays, production downtime and line idling can occur which would bear a detrimental effect on finances and on the equilibrium of the production process.
iv. The organization would not be able to meet an unexpected increase in orders due to the fact that there are no excess finished goods.
v. Transaction costs would be relatively high as frequent transactions would be made.
vi. Just-in-time manufacturing may have certain detrimental effects on the environment due to the frequent deliveries that would result in increased use of transportation, which in turn would consume more fossil fuels.
Precautions to be Taken while Adopting Just in Time technique:
Following are the things to remember while implementing a Just-In-Time Manufacturing System:
i. Management buy-in and support at all levels of the organization are required; if a just-in- time manufacturing system is to be successfully adopted.
ii. Adequate resources should be allocated, so as to obtain technologically advanced software that is generally required if a just-in-time system is to be a success.
iii. Building a close, trusting relationship with reputed and time-tested suppliers will minimize unexpected delays in the receipt of inventory.
iv. Just-in-time manufacturing cannot be adopted overnight. It requires commitment in terms of time and adjustments to corporate culture would be required, as it is starkly different to traditional production processes.
v. The design flow process needs to be redesigned and layouts need to be reformatted, so as to incorporate just-in-time manufacturing.
vi. Lot sizes need to be minimized,
vii. Workstation capacity should be balanced whenever possible.
viii. Preventive maintenance should be carried out, so as to minimize machine breakdowns,
ix. Set-up times should be reduced wherever possible.
x. Quality enhancement programs should be adopted, so that total quality control practices can be adopted.
xi. Reduction in lead times and frequent deliveries should be incorporated.
xii. Motion waste should be minimized, so the incorporation of conveyor belts might prove to be a good idea when implementing a just-in-time manufacturing system.
Just-in-time manufacturing is a philosophy that has been successfully implemented in many manufacturing organizations. It is an optimal system that reduces inventory whilst being increasingly responsive to customer needs; this is not to say that it is not without its pitfalls.
However, these disadvantages can be overcome with a little forethought and a lot of commitment at all levels of the organization.
Technique # 9. Ved Analysis:
VED Analysis attempts to classify the items used into three broad categories, namely Vital, Essential, and Desirable. The analysis classifies items on the basis of their criticality for the industry or company. Vital essential and desirable analysis is used primarily for the control of spare parts.
(i) Vital
Vital category items are those items without which the production activities or any other activity of the company, would come to a halt, or at least be drastically affected. The items the stock out of which even for a short time will stop production for quite some time and future are known as vital category items.
(ii) Essential
Essential items are those items whose stock – out cost is very high for the company. The items stock out of which even for a few hours of days and cost of lost production is high is called essential.
(iii) Desirable
Desirable items are those items whose stock-out or shortage causes only a minor disruption for a short duration in the production schedule. The cost incurred is very nominal. These are the items which are needed but their absence for even a week or so will not lead to stoppage of production.
Top 8 Benefits of Inventory Management
Benefits of Inventory Management are as follows:
(a) Inventory control ensures an adequate supply of materials, stores etc.
(b) It keeps down investment in inventories, inventory carrying costs and obsolescence losses to the minimum.
(c) It eliminates duplication in ordering or in replenishing stocks by centralizing the source from which purchase requisitions emanate.
(d) It provides a check against the loss of materials through carelessness or pilferage.
(e) It facilitates cost accounting activities by producing a means for allocating material costs to products, departments or other operating accounts.
(f) It enables management to make cost and consumption comparisons between operations and periods.
(g) It serves as a means for identifying and disposal of inactive and obsolete items of stores.
(h) Perpetual inventory values provide a consistent and reliable basis for preparing financial statements.
Inventory Management – Significant Problems (With Contrary Demands Required by Inventory Managers)
The inventory theory deals with the determination of optimal procedures for the procurement of the stocks of commodities to meet future demand.
There are different inventory problems, each varying from situation to situation which may be summed up as under:
(i) Knowledge of demand, certainty, risk and uncertainty;
(ii) Method of obtaining a commodity;
(iii) The decision process;
(iv) Analytical conveniences; fixed demand distribution over a period of time or varying demand distribution;
(v) Time lag in receiving an order – constant time lag or probability distribution.
An analysis of inventory problems is fundamentally based on very simple, common sense observations-that in any genuine inventory problem whatsoever, there must be opposing costs.
By this, we may think simply that there is a cost associated with doing “too large” and there is a cost associated with doing “too little”. Sometimes, there are several such costs; but there must always be at least one in each direction.
Conventional organisations treat the materials department as a cost centre. Its efficiency is measured by the cost of service it performs rather than by contribution to profit. This attitude has obviously meant a low status for materials management.
The integrated management activity need no longer be treated as a cost centre whose contribution is measured by whether or not it serves other departments. If the materials department is treated as a profit centre, it can significantly contribute to corporate earnings.
In a company, raw materials and consumable stores are usually transferred from the materials department to the production department. If an item is purchased for Rs.10, it is assumed that the cost of raw material for the production department is Rs.10.
This is incorrect. Implicit in this costing is the assumption that no value is added to distribution during the stage covered by the materials management.
The department invests the company’s capital and incurs certain overheads. The real cost of the item delivered to the production department is always more. If any management does not accept this view, it should not block its funds in inventory which is stored in the materials department.
It is obvious that no company can afford to operate without inventory. When the materials department transfers materials to the production department at a price which is more than its total allocated costs, it is said to function as a profit centre.
Many paradoxical demands are made on those who manage or influence the level of marketing inventories; these demands serve to underscore the need for a deft handling of inventory.
For some of the seemingly contrary demands which are met, the inventory managers have to:
(i) Keep stocks at a low level, but not too low;
(ii) Make stocks, keep pace with the sales;
(iii) Increase turnover;
(iv) Make volume purchases;
(v) Obtain better prices but avoid over-buying;
(vi) Maintain a good assortment of products but not too many;
(vii) Give particular attention to high margin inventory items, but not lose sight of those low margin products with high turnover rates;
(viii) Dispose of obsolete items.
The very nature and dimension of inventories make them suitable for electronic data processing (EDP) handling. Managers of inventory programmes implemented by EDP can provide a maximum service to the higher management, if they know the economic factors which affect the inventories they control.
It would be a tragic and lonely road for them to traverse if they set themselves apart organisationally, while the management dedicates its efforts to the integration of its functional forces. However, the bottleneck in most inventory control procedures is data inputs and their utilisation.
Many inventory management decisions have been reduced to formulae, some of which are very simple. Whenever some decisions can be reduced to routine operations, the human mind is freed from tedious, repetitive routines and concentrates on more important decision-making, including the determination of optimum routines and a well-balanced set of objectives.
The statistical tools enable the inventory manager to exercise better judgement and to capitalise more effectively on his experience. Most inventory principles, problems, decisions and procedures are concerned with the interaction of many variable values – quantities, space, prices, costs and distances.
These variables are related, some according to very definite patterns and others in a loose manner. The interactions of these variables tend to follow mathematical and statistical patterns. They are functionally related.
But mathematics alone, useful and powerful as it is, cannot manage any more than a saw and chisel can make a table. But inventory management and cabinet-making call for human application, not only of appropriate tools but also of judgement and skill.
An understanding of the EOQ principle and the ability to translate that principle into workable operating procedures are necessary for a successful use of the powerful tool of economic lot purchases. Equally important is the control of the tool to meet particular system objectives.
The application of EOQ sometimes fails because the members of an organisation do not grasp the economical and mathematical principles on which it rests or cannot solve the practical problems of data gathering and formula computation.
Very often, the application fails because the inventory manager is dissatisfied with the resulting ordering rates and inventory levels, and is unable to control the operations to achieve satisfactory results.
The success of economic lot purchase requires the inventory manager to:
(i) Set objectives of economic lot purchasing;
(ii) Predict the consequences in terms of ordering rate and inventory levels, of using particular values of order cost and holding rate in the EOQ expression; and
(iii) Select the values that most closely meet stated objectives.
The term ‘Inventory’ refers to the stock of raw materials, spare parts and finished products held by a business firm. It is the aggregate quality of materials, resources and goods that are idle at a given point of time.
Inventory management refers to the process of managing the stocks of finished products, semi-finished products and raw materials by a firm. Inventory management, if done properly, can bring down cost and increase the revenue of a firm.
The inventory management process begins as soon as the firm has started production and ordered raw materials, semi-finished products or any other thing from a supplier. Once orders have been placed, there is generally a short period of time available to the firm to put an inventory management plan in place before the supplies are delivered.
Inventory management helps the firm to decide in advance where these supplies should be stored. If the firm is getting supplies of small- sized goods, it may not be much of a problem to store them, but in the case of large goods, one has to be careful so that the warehousing space is optimally utilised.
Contents
- Introduction to Inventory Management
- Meaning and Definition of Inventory
- Meaning of Inventory Management
- Objectives of Inventory Management
- Purpose of Inventory Management
- Importance of Inventory
- Importance of Inventory Management
- Classification of Inventories
- Types of Inventory
- Norms of Inventory
- Motives for Holding Inventory
- Costs of Holding Inventories
- Factors Influencing Inventory Management
- Economic Order Quantity
- Role of Financial Manager In Inventory Management
- Techniques of Inventory Management
- Benefits of Inventory Management
- Significant Problems of Inventory Management
What is Inventory Management: Introduction, Meaning, Definition, Objectives, Purpose, Importance, Classification, Types, Techniques, ABC Analysis, Norms, Motives, Factors and More…
Inventory Management – Introduction
A large part of total assets of a business is found in the form of inventory. To observe that the investment in inventory is not unnecessarily high, management should keep proper control on the amount and structure of inventory.
Because among all the current assets of business, inventory is the least liquid, any wrong in the management of inventory cannot be corrected easily and it can be very costly for the firm. Funds of the firm which are procured from internal as well as external sources need to be managed inventory and for this purpose inventory should be aware of all the factors affecting the level of management and the methods to control it.
The main objective of inventory management is to determine the level for each type of inventory. For this purpose the purchasing and carrying costs should be compared with their benefits. For example- when a firm purchases in bulk quantity, it’s out of stock costs and risk decreases but in case it continues to purchase, it reaches a point where it’s carrying costs exceed its benefits.
Therefore, the management should maintain only a proper level of inventory. Not only the financial manager is concerned with inventory management, but it also affects marketing and production managers. For determining an optimum level of inventory, proper coordination among all of them is essential.
Inventory is a current asset. Inventory means the goods which are kept for sale during the general operation of business. In case of trading institution it includes only finished goods.
In manufacturing concerns inventory may include:
(i) Inventory of Raw Material
(ii) Inventory of Work-in-Progress
(iii) Inventory of Finished Goods
(iv) Stores and Supplies.
In raw material, such goods are included which are converted into finished goods with the help of the production process. It is an important constituent of the cost of finished products. In the semi-finished goods all those goods are included which are in different stages of production processes and some process is to be employed to convert it into finished product.
After the completion of the manufacturing process, semi- finished goods are converted into finished products. Thus, finished goods are those goods on which the manufacturing work is complete and available for sale. Stores and supplies include fuel, coal, cotton, lubricant oil, broom, chemicals, etc.
The stores do not enter into the production process directly but are needed to run the production process smoothly and constitute an average small part in the total investment. Raw material and semi-finished goods help in the process of production and finished goods inventory helps in fulfilling the demand of customers.
The quantity of each type of inventory is different depending on the nature of different businesses.
For example- in a firm engaged in manufacturing activity, the level of all types of inventory will be high. But in a trading business, like wholesale or retail trade, the stock of finished products will be high but there will be no stock of work-in-progress, raw material and stores and supplies.
Inventory can be financed out of short term loans from banks but it will affect interest charges. Cost of inventory and interest charges can be reduced by proper inventory planning and control.
Inventory Management – Meaning and Definition of Inventory
The term ‘Inventory’ refers to the stock of raw materials, spare parts and finished products held by a business firm. It is the aggregate quality of materials, resources and goods that are idle at a given point of time.
The resources may be of any type; for example men, materials, machines or money when the resources involved in materials or goods in any stage of completion, inventory referred to as stocks. Hence, inventory refers to the ‘stocks’ that a business firm keeps to meet its future requirement of production and sales.
In financial parlance, Inventory is defined as the sum of the value of raw materials, fuels and lubricants, spare parts, maintenance consumables; semi processed materials and finished goods stock at any given point of time.
Inventories are maintained basically for the operational smoothness which they can affect by uncoupling successive stages of production, whereas the monetary value of inventory serves as a guide to indicate the size of the investment made to achieve this operational convenience.
Inventory Management – Meaning
Inventory management refers to the process of managing the stocks of finished products, semi-finished products and raw materials by a firm. Inventory management, if done properly, can bring down cost and increase the revenue of a firm.
The inventory management process begins as soon as the firm has started production and ordered raw materials, semi-finished products or any other thing from a supplier. Once orders have been placed, there is generally a short period of time available to the firm to put an inventory management plan in place before the supplies are delivered.
Inventory management helps the firm to decide in advance where these supplies should be stored. If the firm is getting supplies of small- sized goods, it may not be much of a problem to store them, but in the case of large goods, one has to be careful so that the warehousing space is optimally utilised.
From invoices to purchase orders, the purchase manager has to do a lot of paperwork and documentation involved in inventory management. Although the purchase manager is personally responsible to take care of inventory of the firm, the finance manager has to play an active role in the management of inventory. He, in fact, is the decision maker in the whole process of inventory management.
Any firm would like to keep higher levels of inventory. This will enable the firm to be more flexible in supplying to the customers and will find ease in its production schedule. Most of the customers may require immediate delivery and higher inventories may help meeting their demands and hence there would be less and less chances of sales being disrupted.
But there is always a cost involved in the inventory. This cost, as mentioned earlier, includes the capital cost of the stock and the costs of storing and carrying etc. On the other hand, holding a lower level of stock than required may result in stock-outs.
The cost of stock-out may be sales loss or customer dissatisfaction. The stock-outs may also result in delays or hold ups in the production process.
Given the benefits of holding inventory and cost of stock-outs, the firm will be tempted to hold maximum possible inventory. But this is costly too, because the funds blocked in inventory always have an opportunity cost. So the firm has to avert both overstocking as well as under stocking and determine an optimum level of inventory in such a way as to get the best return thereof.
It must weigh the benefits of holding inventory against its opportunity cost. While determining the optimum level of inventory, the firm has to take necessary steps to reconcile the differing viewpoints of production manager, marketing manager and the finance manager.
No doubt, most of the decisions relating to inventory are taken by the purchase manager in consultation with the production manager. Still the finance manager should ensure that the inventory is properly controlled and he should stress the need for the consideration of financial implications of inventory management.
Thus the inventory management focuses on determining and maintaining an optimum level of inventory in the firm. The inventory management seeks to maximise the wealth of the shareholders by designing and implementing such policies which attempt to minimise the cost of procuring and maintaining the inventory.
Inventory Management – Objectives
Objectives of Inventory Management are:
Through the efficient management of inventory the wealth of owners will be maximised. To reduce the requirement of cash in business, inventory turnover should be maximised and management should save itself from the loss of production and sales, arising from its being out of stock.
On the one hand, management should maximise stock turnover so that investment in inventory could be minimised and on the other hand, it should keep adequate inventory to operate the production and sales activities efficiently.
The main objective of inventory management is to maintain inventory at an appropriate level so that it is neither excessive nor short of requirement.
Thus, management is faced with two conflicting objectives:
(i) To keep inventory at sufficiently high level to perform production and sales activities smoothly.
(ii) To minimise investment in inventory at minimum level to maximise profitability.
Both inadequate and excessive quantities of inventory are undesirable for business. These mutually conflicting objectives of inventory management can be explained in the form of costs associated with inventory and the profits accruing from it.
Low quantum of inventory reduces costs and high level of inventory saves business from being out of stock and helps in running the production and sales activities smoothly.
The objectives of inventory management can be explained in detail as under:
(i) To ensure that the supply of raw material and finished goods will remain continuous so that the production process is not halted and the demands of the customers are duly met.
(ii) To minimise the carrying costs of inventory.
(iii) To keep investment in inventory at the optimum level.
(iv) To reduce the losses of theft, obsolescence and wastage, etc.
(v) To make arrangements for the sale of slow moving items.
(vi) To minimise inventory ordering costs.
Top 5 Purpose of Inventory Management
Purpose of Inventory Management are as follows:
1. To meet expected demand of the market intermediaries and end users.
2. Take advantage of Price Increase and Quantity Discounts.
3. To allow flexibility in production scheduling.
4. To seek protection from variation in raw material delivery time.
5. Reduce Transit Cost and duration.
Inventory Management – Top 4 Importance of Inventory
Importance of Inventory are as follows:
1. For smooth running of business operations inventory is indispensable. The prime components of business operations are production and marketing. Inventory establishes a very important linkage between the two.It separates both production and marketing and sets up coordination between the two.
Thus, production operations continue without any marketing barrier and marketing becomes effective without any production barrier.
2. Operation of each business concern is greatly affected by market factors especially the changes in demand. At the same time, the changes caused by trade cycles also affect the life of the business. If the concern continues production and marketing in a systematic way, it cannot bear with these changes.
There is a need to keep some finished goods as inventory, so that reconciliation can be made in accordance with the changes in demand. In this way inventory provides a cushion against the losses arising out of changes in demand or cyclical changes.
3. Since inventory by setting coordination between production and marketing makes production and distribution more easy and constant, the stability in employment in the business concern becomes possible.
In the absence of inventory, sometimes production has to be curtailed and sometimes production has to be increased. In both the situations, employment-status would tend to fluctuate. Thus, inventory helps in making employment comparatively stable.
4. In most of the business concerns, inventory forms the largest component of working capital. Inventory as a component of working capital is helpful in earning the profit. It is the inventory through which some profits can be earned.
Rest components of working capital are in liquid form fetching very minimum or zero profit. It has been proved that inventory turnover affects the rate of return.
Importance of Inventory Management
Inventory management covers a large number of problems including fixation of minimum and maximum levels, determining the size of inventory to be carried, deciding about the issue, receipts and inspection procedures, determining the Economic Order Quantity, proper storage facilities, keeping check over obsolescence and ensuring control over movement of inventories.
The importance of the inventory management is summarised as follows:
i. Transaction Motive to Avoid Loss Related to the Gap between the Demand and Supply of Goods:
As and when the demand for the product arises, the firm has to deliver goods. The stock of RM and WIP is also needed for an efficient and smooth production run. If demand has to be met in time, the goods from the plant have to be supplied in time.
Thus adequate inventory of RM, WIP and FGs is needed to manufacture the product, allow smooth flow of material and the final product in the production process and distribution cycle of the firm to match the predicted demand and related supply of the product.
ii. Gaining Quantity Discounts:
The firm purchases and stores material during favourable economic conditions in order to minimise the cost of material input. Suppliers usually give trade discounts on bulk purchases by customers. Thus, the firm gains from discount on the bulk purchases of material inputs. This decreases the overall cost to the firm.
iii. Reduction in Ordering Cost:
The costs involved between the time of placing the order and receiving the supply of goods ordered which are then inspected and counted before final payment are known as operating cost. Operating costs are independent of the size of order.
Hence, if the firm increases the size of its order and thus decreases the frequency of its order, its Operating Cycle is reduced, reducing the overall cost to the firm.
iv. Efficiency and Economy of Production Run:
There are certain costs in starting the machine to run the production process. These costs are termed as start-up costs. Start-up cost is independent of the length (time duration) of production run.
Thus, if the firm increases its production run (i.e., for a longer time period) and thus decreases the frequency of production run, start-up costs are reduced, thereby reducing the overall cost to the firm. Such production runs are said to be efficient and profitable.
v. Precautionary Motive:
Inventory acts as buffer stock. It acts as a shock absorber and co-ordinates the various interdepartmental processes such as – purchasing, production and selling. Adequate inventory of RM and WIP is maintained to run large, efficient and smooth production runs.
vi. Creating Goodwill among Customers:
Meeting customers’ demand in time even in case of errors in forecasted demand creates goodwill and loyalty on part of the customers.
Inventory Management – Classification of Inventories: Raw Material, Component Parts, Work -in Process, Finished Good and Supplies
Classification of Inventories are as follows:
(a) Raw Material
A raw material inventory includes all items that, after being received at the plant, require additional processing before becoming an identifiable part of the finished product.
(b) Component Parts
This classification of inventory is applied to component parts of a product that need no additional processing before being assembled into the finished product. The TV picture tube that is the finished product of one manufacturer becomes a purchased part to the television set manufacturer.
(c) Work -in Process
Work-in-process is the inventory of material, the flow of which is controlled by production control procedures.
(d) Finished Good
This classification applied to the quantities of finished goods that are held at the factory awaiting shipment. In many instances, however, it will include stocks held in warehouses owned and operated by the manufacturer, or stock held on dealers’ floors on consignment.
(e) Supplies
All the materials needed for the operation of the plant that are not used as parts of the finished product are classified as supplies. The material that becomes part of the finished product is called “direct material”.
Inventory Management – Types of Inventory: Raw Materials, Work-In-Process and Finished Goods
Inventories consist of raw material, work-in-process and finished goods which are held by a firm in the ordinary course of business, either for sale or for the purpose of using them in the process of producing goods and services. Inventories constitute the most significant part of current assets for a majority of firms.
There are three types of inventories:
1. Raw materials,
2. Work-in-process and
3. Finished goods.
1. Raw Materials:
This type of inventory includes direct materials that are used in the manufacture of a product, or the components that are used to assemble a finished product. Raw materials may also include partially finished goods or materials.
For example, for an ice cream manufacturing firm, milk, sugar and preservatives are raw materials; while for a computer manufacturer, chips, circuit boards and transistors are raw materials. Inventory items may be classified as raw materials if the organization has purchased them from an outside firm, or if they are used to make components.
2. Work-In-Process:
This includes the partially completed goods, parts, or sub-assemblies that are not yet part of the finished product inventory and no longer form part of the raw materials inventory. Work-in-process inventory forms a part of the current assets of a firm and is valued usually at lower cost and realizable value by following the accounting principle of conservatism.
This is also known as work-in-progress that includes partly finished goods and materials, sub-assemblies, etc., which are held in between the stages of production; the stock of goods, which are partly processed and are still in the process of production; the partially assembled items; finished goods that have not yet been packaged and inspected, and also the raw materials that have moved from storage to a pre-assembly area.
For example, in an ice cream firm, the milk may come into a storage area, where they are raw material, but once they have been moved out of the storage area and onto the assembly line for making ice cream, they become work-in-process inventory.
If a business makes and sells chairs, work-in-process inventory would include any unfinished chairs. In a small firm, work-in-process goods may be stored in the same area as raw materials and finished goods.
3. Finished Goods:
Finished goods are all those items of products that are fit for sale and ready to be shipped out or sold directly to customers, including to wholesalers and retailers. Finished goods may be waiting in a storage area or on a shop floor.
If the amount of inventory of finished goods increases faster than the amount of raw goods and work-in-process goods, then production may need to slow down until more finished goods are sold. In some businesses, where goods are made to order, goods are not included in the finished goods inventory until they are sold.
In manufacturing concerns, there are usually three types of inventory as explained above. However, the only form of inventory, in case of retailers and distributors, are finished goods. For example, in a retail business that buys and sells toys, the unsold items of the toys constitute the inventory of finished goods.
For service concerns, inventory is any supply that is used up to provide the services. For instance, a beauty saloon’s inventory includes various cosmetics that are used during its service to the clients.
Apart from these, other types of inventory include maintenance, repair and operating items. These include all the items that an organization needs to operate, for example, office equipment, packing boxes and loose tools to repair equipment. There are also other types of inventory that are classified on the basis of the purpose they serve.
These include transit inventory, which are products or components that are being moved from one location to another, such as from a warehouse to a factory; buffer inventory, which are excess inventory items that are kept on hand to protect against supply problems.
Some of these problems are poor quality materials, slower delivery of raw materials and maintenance of anticipatory inventory, which are stocked to meet any excess demand.
For instance, during the festive season of Diwali, demand for consumer goods is quite high. Therefore, sellers maintain high inventory levels to meet the excess demand.
Inventory Management – Norms of Inventory
The norms are the limits for inventory could be set by either the top management, or the materials management department. The top management usually sets monetary limits for investment in inventories.
The materials department then has to allocate this investment to the various items and ensure the smooth operation of the company. It would be worthwhile if the inventory norms are set by the “management by objectives” concept.
In the setting up of the norms, the involvement of persons who are directly responsible for maintaining the inventories is very desirable. Other departments involved in setting the norms are finance, production, marketing and materials control.
The norms of inventory should be converted to specially spell out parameters like the number of stock outs permitted, the sales to inventory ratio and inventory to consumption ratio.
Inventory Management – Top 3 Principal Motives for Holding Inventory: Transaction Motive, Precautionary Motive and Speculative Motive
Like cash, there are three principal motives for holding inventory:
a) Transaction Motive:
It facilitates uninterrupted production & delivery of order at a given right time. This motive means holding inventory for satisfying sales and production requirements. Normally, every production process takes some time.
When the customers come for purchase, the firm needs ready goods so that it can deliver them to customers on time. If the firm does not have ready finished goods, and the customer needs goods immediately, the firm would not be able to supply on time.
Therefore some amount of finished goods must be kept ready so that sales are not lost. Similarly, in the production process, the factory may demand raw materials continuously. If the firm does not have ready stock of raw material, then it will order for purchase.
Till the raw materials arrive, it may have to stop its production process. Therefore, in order to keep the production process uninterrupted, raw materials stock has to be kept. The same logic can be applied on WIP inventory at different stages of the production process.
b) Precautionary Motive:
It is for unexpected changes in demand and supply factors. Inventory kept with precautionary motive is kept to act as a buffer if the actual level of activity (sales or production) exceeds the planned or anticipated levels.
Again, this motive is applicable to all types of inventory viz. raw material, work in process and finished goods. For example, a restaurant keeping extra supplies to meet extra demand on Saturday and Sundays.
c) Speculative Motive:
This motive means keeping large stocks in anticipation of change in prices that would enable the firm to take advantage of changes in prices and getting quantity discounts. This motive also works when the firm is anticipating a change in the product.
i. Inventory Holding-
Practical Considerations- These motives are the theoretical explanations for holding stock. But in reality, inventory serves the “decoupling” purpose. What is decoupling? It means making two processes independent of each other. For example, holding raw material inventory will decouple production and purchase functions.
If we do not hold any raw material inventory, what will happen? Then every time there is a requirement of raw material in the factory (production process), immediate purchase will be needed. The production process will “depend” on the purchase to run smoothly.
But by keeping raw material stock, we decouple the production and purchase process. The production runs smoothly even if purchase of materials is taking time. Need a policy for balanced investment in inventory including excessive (dangers), inadequate (dangers).
Similarly, WIP inventory acts to decouple various stages of the production process. One stage of the production process becomes independent of the previous stage if some WIP inventory is kept from the previous stage.
Likewise, the Finished goods inventory decouples selling & distribution from production. If finished goods are readily available in stock, the marketing team does not need to consult the production department before committing supply of an order.
Inventory Management – Costs of Holding Inventories
When a firm holds goods for future sale, it exposes itself to a number of risks and costs. The effective management of inventory involves a trade-off between having too little and too much inventory. In achieving this trade-off, the financial manager should realise that risks and costs may be closely related.
The costs of holding inventories are as follows:
1. Material Costs:
These are the costs of purchasing the goods plus transportation and handling. This may be calculated by adding the purchase price (less and discounts), the delivery charges and the sales tax (if any).
2. Order Costs:
These are the variable costs of placing an order for the goods. Each separate shipment involves certain expenses connected with requesting and receiving materials.
Examples of these costs are the typing of the order and the inspection of the goods after they arrive. The fewer the orders, the lower the order cost will be for the firm.
3. Carrying Costs:
These are the expenses of storing goods. Once the goods have been accepted, they become part of the firm’s inventories.
The following are the examples of different kinds of carrying costs:
i. Storage Costs
The firm must provide for storage space, usually through the operation of a warehouse or supply room. The firm must employ workers to move, clean, count, record and protect the goods. All of these activities dealing with the physical holding of the goods are considered storage costs.
ii. Insurance
In spite of the best precautions taken, firms must protect themselves against such hazards as fire or accidents in the warehouse. Larger amounts of inventory require larger amounts of insurance. The insurance premiums represent a carrying cost on inventory.
iii. Obsolescence and Spoilage
When firms hold goods, they expose themselves to the possibility that the goods will not be saleable when the time arrives. Obsolescence is the cost of being unable to sell goods because of current market factors deriving from changes in styles, tastes or other factors.
If a product is no longer wanted, the firm must sell it at a fraction of its value or destroy it. Spoilage occurs when a product is not saleable because of deterioration during the storage, such as – foods that rot, plants that die, garments that are attacked by moths, candles that discolour or chemicals that decompose.
iv. Damage or Theft
Although a firm makes every effort to protect goods against damage and safeguard items against pilferage, goods are damaged and stolen. A portion of these expenses are not covered by insurance and are losses to the firm. Some businesses, particularly retail stores and firms producing luxury goods, face this carrying cost.
4. Cost of Funds Tied up in Inventory:
Whenever a firm commits its resources to inventory, it is using funds that Otherwise might be available for other purposes. A portion of the inventory is financed by trade credit from suppliers and involves no cost.
The balance of the inventory must be financed from the firm’s general funds and involves a cost. If the firm is considering an expansion of inventory and plans to borrow to obtain funds, the firm will have to pay interest on the additional debt.
5. Cost of Running Out of Goods:
Whenever a firm incurs shortages of products, it incurs costs. If the firm is unable to fill an order, it risks losing a sale. If the firm runs out of raw materials, it may force a costly shutdown of the production process. Adequate inventory helps reduce additional costs and lost revenues due to shortages.
Factors Influencing Inventory Management
Factors Influencing Inventory Management are as follows:
Many factors influence inventory management and control. The principal effects of these factors are reflected most strongly in the levels of inventory and the degree of control planned in the inventory control system. The factors include type of product, type of manufacture, volume of output and others.
(a) Type of Product:
If the materials used in the manufacture of the product have a high unit value when purchased, a much closer control is usually in order. If the material used in the product is in short supply or is rationed by the government, this may influence the purchase of this material and stock maintained.
Material required to product made-to-order items needs strict control to ensure that no item is lost in the process of manufacture. Such materials are of special and expensive type and a loss of any small part will hold the production.
(b) Type of Manufacture:
Continuous manufacture is common to the manufacture of standard products. However, some standard products are made in batches. Where continuous manufacture is employed, the rate of production is the key factor.
Here inventory control is of major importance and in reality controls the production of the product. The economic advantage of this type of manufacture is the uninterrupted operation of the machines and assembly lines in the plant.
(c) Volume of Product:
The volume of product to be made, as represented by the rate of production, may have little effect on the complexity of the inventory problem. Literally millions of brass bases for light bulbs are manufactured, even money involving the control of only two principal items of raw materials inventory.
(d) Other Factors are:
- The potential savings that might be anticipated from improved control of inventories.
- The nature and size of inventories and their relationship to other functions in the company, such as manufacturing, finance, marketing etc.
- The objectives of the company as they relate to inventories and the level of service to be provided to customers.
- The current, or potential, availability of data that can be used in controlling inventories.
- The present method for controlling inventories and for making inventory decisions.
Inventory Management – Economic Order Quantity (With Assumptions)
Stocks are held to satisfy demands quickly to allow unimpeded production, to take advantage of bulk purchasing, as a necessary part of the production process, and to absorb seasonal and other fluctuations.
However, stocks accumulate unnecessarily through poor control methods, obsolescence, poor liaison and sub-optimal decision making. One basic inventory control system is called the re-order level under which the usual replenishment order quantity is the EOQ (economic order quantity).
This ordering quantity minimizes the balance of cost between inventory holding costs and re-order costs. The prime objective of inventory management is to find out and maintain optimum level of investment in inventory to minimize the total costs associated with it.
The EOQ is the optimum size of the order for a particular item of inventory calculated at a point where the total inventory costs are at a minimum for that particular stock item.
It is an optimum size of either a normal outside purchase order or an internal production order that minimizes total annual holding and ordering costs of inventory. Stock-out costs are difficult to incorporate into this model.
Since they are based on qualitative and subjective judgment. The ordering costs are the costs of placing a separate order multiplied by the number of separate orders placed in the period.
The carrying costs can be calculated based on the assumption that the annual cost of carrying a particular stock item on average, half the stock is on hand all the time in addition to the safety or buffer stock.
The fewer the orders, the lower costs of ordering, but the greater the size of the order the greater the costs of carrying. The safety or buffer stock has no bearing on the EOQ, only on the timing of orders.
Assumptions of EOQ:
To be able to calculate a basic EOQ certain assumptions are necessary:
a. That there is a known, constant stock holding cost.
b. That there is a known, constant ordering cost.
c. That rates of demand are known and constant.
d. That there is a known, constant price per unit, i.e., there are no price discounts.
e. That replenishment is made instantaneously, i.e., the whole batch delivered at once.
Role of Financial Manager In Inventory Management – Inventory Turnover Ratio and Ageing Schedule of Inventory
In the preceding section, the costs and benefits associated with inventories have been discussed. The financial manager shall be aware of advantages and disadvantages associated with high level and low level of inventories.
The financial manager can arrive at the optimum quantity of inventories to be ordered by using the EOQ model. The model helps in determining the optimum size of the order but another issue relating to time for placing the order is sorted out by evaluating reorder level.
The financial manager on the basis of his past experience can estimate the time usually taken by suppliers to deliver the inventories after placement of an order i.e., lead time. Thus, using lead time and safety stock, reorder level can be ascertained.
Besides the evaluation of order size of inventories and timing for placing order for inventories, the financial manager shall take care of maintaining inventories for which ABC system/analysis criteria may be used in addition to these techniques, the financial manager shall use inventory turnover ratio and ageing schedule of inventory which are briefly discussed below:
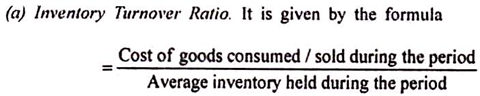
The ratio helps in determining the amount of investment to be made in various kinds of inventories being maintained by the firm.
On the basis of ratio, inventories are classified into four types:
(i) Slow moving inventories
(ii) Fast moving inventories
(iii) Dormant inventories
(iv) Obsolete inventories.
The firm makes more investment in fast moving inventories and pays less attention to slow moving inventories. Dormant inventories are those inventories which have no demand and they are to be returned back to the suppliers or disposed of in the market at salvage value. Sometimes, they may be retained if the financial manager expects their demand in future.
(b) Ageing Schedule of Inventory
The financial manager shall determine the time lag between the date of purchase of inventories and the date of their usage for production purpose. This will help in identifying the rate at which various inventories are consumed.
Using this information, the inventory manager will be able to take adequate steps while purchasing inventories so that inventories do not get deteriorated before they are consumed for the production process.
Techniques of Inventory Management
Some of the most important techniques of inventory Management are discussed below:
Technique # 1. Setting Up of Various Stock Levels:
To avoid over-stocking and understocking of materials, the management has to decide about the maximum level, minimum level, re-order level, danger level and average level of materials to be kept in the store.
These terms are explained below:
(i) Re-Ordering Level:
It is also known as – ‘ordering level’ or ‘ordering point’ or ‘ordering limit’. It is a point at which order for supply of material should be made. This level is fixed somewhere between the maximum level and the minimum level in such a way that the quantity of materials represented by the difference between the re-ordering level and the minimum level will be sufficient to meet the demands of production till such time as the materials are replenished.
Reorder level depends mainly on the maximum rate of consumption and order lead time. When this level is reached, the store keeper will initiate the purchase requisition.
Reordering level is calculated with the following formula:
Re-order level = Maximum rate of consumption x maximum lead time
(ii) Maximum Level:
Maximum level is the level above which stock should never reach. It is also known as ‘maximum limit’ or ‘maximum stock’. The function of maximum level is essential to avoid unnecessary blocking up of capital in inventories, losses on account of deterioration and obsolescence of materials, extra overheads and temptation to thefts etc.
This level can be determined with the following formula:
Maximum Stock level = Reordering level + Reordering quantity – (Minimum Consumption x Minimum re-ordering period)
(iii) Minimum Level:
It represents the lowest quantity of a particular material below which stock should not be allowed to fall. This level must be maintained at every time so that production is not held up due to shortage of any material. It is that level of inventories of which a fresh order must be placed to replenish the stock.
This level is usually determined through the following formula:
Minimum Level = Re-ordering level – (Normal rate of consumption x Normal delivery period)
(iv) Average Stock Level:
Average stock level is determined by averaging the minimum and maximum level of stock.
The formula for determination of the level is as follows:
Average level =1/2 (Minimum stock level + Maximum stock level)
This may also be expressed by Minimum level + 1/2 of Re-ordering Quantity.
(v) Danger Level:
Danger level is that level below which the stock should under no circumstances be allowed to fall. Danger level is slightly below the minimum level and therefore the purchases manager should make special efforts to acquire required materials and stores.
This level can be calculated with the help of following formula:
Danger Level = Average rate of consumption x Emergency supply time.
(vi) Economic Order Quantity (E.O.Q.):
One of the most important problems faced by the purchasing department is how much to order at a time. Purchasing in large quantities involves lesser purchasing cost. But the cost of carrying them tends to be higher. Likewise if purchases are made in smaller quantities, holding costs are lower while purchasing costs tend to be higher.
Hence, the most economic buying quantity or the optimum quantity should be determined by the purchase department by considering the factors such as cost of ordering, holding or carrying.
This can be calculated by the following formula:
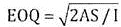
Where A stands for annual requirements of an item in terms of rupees;
S stands for cost of placement of an order in rupees; and
I stand for inventory carrying cost per unit per year in rupees.

Storage (holding) cost per unit = cost per unit x Storage cost (%)
Technique # 2. Preparation of Inventory Budgets:
Organizations having huge material requirements normally prepare purchase budgets. The purchase budget should be prepared well in advance. The budget for production and consumable material and for capital and maintenance material should be separately prepared.
Sales budgets generally provide the basis for preparation of production plans. Therefore, the first step in the preparation of a purchase budget is the establishment of a sales budget.
As per the production plan, material schedule is prepared depending upon the amount and return contained in the plan. To determine the net quantities to be procured, necessary adjustments for the stock already held is to be made.
They are valued at standard rate or current market price. In this way, the material procurement budget is prepared. The budget so prepared should be communicated to all departments concerned so that the actual purchase commitments can be regulated as per budgets.
At periodic intervals actuals are compared with the budgeted figures and reported to management which provides a suitable basis for controlling the purchase of materials.
Technique # 3. Maintaining Perpetual Inventory System:
This is another technique to exercise control over inventory. It is also known as an automatic inventory system. The basic objective of this system is to make available details about the quantity and value of stock of each item at all times. Thus, this system provides a rigid control over stock of materials as physical stock can be regularly verified with the stock records kept in the stores and the cost office.
Technique # 4. Perpetual Inventory Control System:
In a large business it is essential to have information about continuous availability of different types of materials and stores purchased, issued and their balance in hand. The perpetual inventory control system enables the manufacturer to know about the availability of these materials and stores without undergoing the cumbersome process of physical stock taking.
Under this method, proper information relating to receipt, issue and materials in hand is kept. The main objective of this system is to have accurate information about the stock level of every item at any time.
Perpetual inventory control system cannot-be successful unless and until it is accompanied by a system of continuous stock taking i.e., checking the total stock of the concern 3 or 4 times a year by picking 10 or 15 items daily (as against physical stock taking which takes place once a year).
The items are taken in rotation. In order to have more effective control, the process of continuous stock taking is usually undertaken by a person other than the storekeeper. This will check the functioning of the storekeeper also.
The items may be selected at random to have a surprise check. The success of the system of perpetual inventory control depends upon the proper implementation of the system of continuous stock taking.
Technique # 5. Establishing Proper Purchase Procedures:
A proper purchase procedure has to be established and adopted to ensure necessary inventory control.
The following steps are involved:
(i) Purchase Requisition
It is the requisition made by the various departmental heads or storekeepers for their various material requirements. The initiation of purchase begins with the receipts of a purchase requisition by the purchase department.
(ii) Inviting Quotations
The purchase department will invite quotations for supply of goods on the receipt of purchase requisition.
(iii) Schedule of Quotations
The schedule of quotations will be prepared by the purchase department on the basis of quotations received.
(iv) Approving the supplier
The schedule of quotations is put before the purchase committee who selects the supplier by considering factors like price, quality of materials, terms of payment, delivery schedule etc.
(v) Purchase Order
It is the last step and the purchase order is prepared by the purchase department. It is a written authorisation to the supplier to supply a specified quality and quantity of material at the specified time and place mentioned at the stipulated terms.
Technique # 6. Inventory Turnover Ratio:
These are calculated to minimise the inventory by the use of the following formula – Inventory Turnover Ratio= Cost of goods consumed or sold during the period/ Average inventory held during the period.
The ratio indicates how quickly the inventory is used for production. Higher the ratio, shorter will be the duration of inventory at the factory. It is the index of efficiency of material management.
The comparison of various inventory turnover ratios at different items with those of previous years may reveal the following four types of inventories:
(i) Slow moving Inventories
These inventories have a very low turnover ratio. Management should take all possible steps to keep such inventories at the lowest levels.
(ii) Dormant Inventories
These inventories have no demand. The finance manager has to make a decision whether such inventories should be retained or scrapped based upon the current market price, conditions etc.
(iii) Obsolete Inventories
These inventories are no longer in demand due to their becoming out of demand. Such inventories should be immediately scrapped.
(iv) Fast moving inventories
These inventories are in hot demand. Proper and special care should be taken in respect of these inventories so that the manufacturing process does not suffer due to shortage of such inventories.
Technique # 7. Abc Analysis:
In order to exercise effective control over materials, A.B.C. (Always Better Control) method is of immense use. Under this method materials are classified into three categories in accordance with their respective values.
Group ‘A’ constitutes costly items which may be only 10 to 20% of the total number of items but account for about 50% of the total value of the stores. A greater degree of control is exercised to preserve these items.
Group ‘B’ consists of items which constitutes 20 to 30% of the store items and represent about 30% of the total value of stores. A reasonable degree of care may be taken in order to control these items.
In the last category i.e., Group ‘C’ about 70 to 80% of the items are covered costing about 20% of the total value. This can be referred to as the residuary category. A routine type of care may be taken in the case of third category.
This method is also known as ‘stock control according to value method’, ‘selective value approach’ and ‘proportional parts value approach’. If this method is applied with care, it ensures considerable reduction in the storage expenses and it is also greatly helpful in preserving costly items.
Technique # 8. Just in Time:
The Just in Time (JIT) method works to lessen the volume of inventory that a business has on hand. It is considered a risky technique because you only purchase inventory a few days before it is needed for distribution, sale or production so that the items arrive just in time for use.
JIT helps organisations save on inventory holding costs by keeping stock levels low, and eliminates situations where deadstock sit on shelves for months on end. One needs to conduct thorough research into customer buying habits, seasonal demand, and source for reliable suppliers and channels of transportation before implementing JIT into a business operations to minimise risks and screw ups.
Advantages:
Just-in-Time Systems:
Following are the advantages of adopting Just-in-Time Manufacturing Systems:
i. Just-in-time manufacturing keeps stock holding costs to a bare minimum. The release of storage space results in better utilization of space and thereby bears a favourable impact on the rent paid and on any insurance premiums that would otherwise need to be paid.
ii. Just-in-time manufacturing eliminates waste, as out-of-date or expired products; do not enter into this equation at all.
iii. As under this technique, only essential stocks are obtained, less working capital is required to finance procurement. Here, a minimum re-order level is set, and once that mark is reached, fresh stocks are ordered making this a boon to inventory management too.
iv. Due to the aforementioned low level of stocks held, the organization’s return on investment (referred to as ROI, in management parlance) would generally be high.
v. As just-in-time production works on a demand-pull basis, all goods made would be sold, and thus it incorporates changes in demand with surprising ease. This makes it especially appealing today, where the market demand is volatile and somewhat unpredictable.
vi. Just-in-time manufacturing encourages the ‘right first time’ concept, so that inspection costs and cost of rework is minimized.
vii. High quality products and greater efficiency can be derived from following a just-in-time production system.
viii. Close relationships are fostered along the production chain under a just-in-time manufacturing system.
ix. Constant communication with the customer results in high customer satisfaction.
x. Overproduction is eliminated when just-in-time manufacturing is adopted.
Disadvantages:
Just in Time Technique:
Following are the disadvantages of Adopting Just-In-Time Manufacturing Systems:
i. Just-in-time manufacturing provides zero tolerance for mistakes, as it makes re-working very difficult in practice, as inventory is kept to a bare minimum.
ii. There is a high reliance on suppliers, whose performance is generally outside the purview of the manufacturer.
iii. Due to there being no buffers for delays, production downtime and line idling can occur which would bear a detrimental effect on finances and on the equilibrium of the production process.
iv. The organization would not be able to meet an unexpected increase in orders due to the fact that there are no excess finished goods.
v. Transaction costs would be relatively high as frequent transactions would be made.
vi. Just-in-time manufacturing may have certain detrimental effects on the environment due to the frequent deliveries that would result in increased use of transportation, which in turn would consume more fossil fuels.
Precautions to be Taken while Adopting Just in Time technique:
Following are the things to remember while implementing a Just-In-Time Manufacturing System:
i. Management buy-in and support at all levels of the organization are required; if a just-in- time manufacturing system is to be successfully adopted.
ii. Adequate resources should be allocated, so as to obtain technologically advanced software that is generally required if a just-in-time system is to be a success.
iii. Building a close, trusting relationship with reputed and time-tested suppliers will minimize unexpected delays in the receipt of inventory.
iv. Just-in-time manufacturing cannot be adopted overnight. It requires commitment in terms of time and adjustments to corporate culture would be required, as it is starkly different to traditional production processes.
v. The design flow process needs to be redesigned and layouts need to be reformatted, so as to incorporate just-in-time manufacturing.
vi. Lot sizes need to be minimized,
vii. Workstation capacity should be balanced whenever possible.
viii. Preventive maintenance should be carried out, so as to minimize machine breakdowns,
ix. Set-up times should be reduced wherever possible.
x. Quality enhancement programs should be adopted, so that total quality control practices can be adopted.
xi. Reduction in lead times and frequent deliveries should be incorporated.
xii. Motion waste should be minimized, so the incorporation of conveyor belts might prove to be a good idea when implementing a just-in-time manufacturing system.
Just-in-time manufacturing is a philosophy that has been successfully implemented in many manufacturing organizations. It is an optimal system that reduces inventory whilst being increasingly responsive to customer needs; this is not to say that it is not without its pitfalls.
However, these disadvantages can be overcome with a little forethought and a lot of commitment at all levels of the organization.
Technique # 9. Ved Analysis:
VED Analysis attempts to classify the items used into three broad categories, namely Vital, Essential, and Desirable. The analysis classifies items on the basis of their criticality for the industry or company. Vital essential and desirable analysis is used primarily for the control of spare parts.
(i) Vital
Vital category items are those items without which the production activities or any other activity of the company, would come to a halt, or at least be drastically affected. The items the stock out of which even for a short time will stop production for quite some time and future are known as vital category items.
(ii) Essential
Essential items are those items whose stock – out cost is very high for the company. The items stock out of which even for a few hours of days and cost of lost production is high is called essential.
(iii) Desirable
Desirable items are those items whose stock-out or shortage causes only a minor disruption for a short duration in the production schedule. The cost incurred is very nominal. These are the items which are needed but their absence for even a week or so will not lead to stoppage of production.
Top 8 Benefits of Inventory Management
Benefits of Inventory Management are as follows:
(a) Inventory control ensures an adequate supply of materials, stores etc.
(b) It keeps down investment in inventories, inventory carrying costs and obsolescence losses to the minimum.
(c) It eliminates duplication in ordering or in replenishing stocks by centralizing the source from which purchase requisitions emanate.
(d) It provides a check against the loss of materials through carelessness or pilferage.
(e) It facilitates cost accounting activities by producing a means for allocating material costs to products, departments or other operating accounts.
(f) It enables management to make cost and consumption comparisons between operations and periods.
(g) It serves as a means for identifying and disposal of inactive and obsolete items of stores.
(h) Perpetual inventory values provide a consistent and reliable basis for preparing financial statements.
Inventory Management – Significant Problems (With Contrary Demands Required by Inventory Managers)
The inventory theory deals with the determination of optimal procedures for the procurement of the stocks of commodities to meet future demand.
There are different inventory problems, each varying from situation to situation which may be summed up as under:
(i) Knowledge of demand, certainty, risk and uncertainty;
(ii) Method of obtaining a commodity;
(iii) The decision process;
(iv) Analytical conveniences; fixed demand distribution over a period of time or varying demand distribution;
(v) Time lag in receiving an order – constant time lag or probability distribution.
An analysis of inventory problems is fundamentally based on very simple, common sense observations-that in any genuine inventory problem whatsoever, there must be opposing costs.
By this, we may think simply that there is a cost associated with doing “too large” and there is a cost associated with doing “too little”. Sometimes, there are several such costs; but there must always be at least one in each direction.
Conventional organisations treat the materials department as a cost centre. Its efficiency is measured by the cost of service it performs rather than by contribution to profit. This attitude has obviously meant a low status for materials management.
The integrated management activity need no longer be treated as a cost centre whose contribution is measured by whether or not it serves other departments. If the materials department is treated as a profit centre, it can significantly contribute to corporate earnings.
In a company, raw materials and consumable stores are usually transferred from the materials department to the production department. If an item is purchased for Rs.10, it is assumed that the cost of raw material for the production department is Rs.10.
This is incorrect. Implicit in this costing is the assumption that no value is added to distribution during the stage covered by the materials management.
The department invests the company’s capital and incurs certain overheads. The real cost of the item delivered to the production department is always more. If any management does not accept this view, it should not block its funds in inventory which is stored in the materials department.
It is obvious that no company can afford to operate without inventory. When the materials department transfers materials to the production department at a price which is more than its total allocated costs, it is said to function as a profit centre.
Many paradoxical demands are made on those who manage or influence the level of marketing inventories; these demands serve to underscore the need for a deft handling of inventory.
For some of the seemingly contrary demands which are met, the inventory managers have to:
(i) Keep stocks at a low level, but not too low;
(ii) Make stocks, keep pace with the sales;
(iii) Increase turnover;
(iv) Make volume purchases;
(v) Obtain better prices but avoid over-buying;
(vi) Maintain a good assortment of products but not too many;
(vii) Give particular attention to high margin inventory items, but not lose sight of those low margin products with high turnover rates;
(viii) Dispose of obsolete items.
The very nature and dimension of inventories make them suitable for electronic data processing (EDP) handling. Managers of inventory programmes implemented by EDP can provide a maximum service to the higher management, if they know the economic factors which affect the inventories they control.
It would be a tragic and lonely road for them to traverse if they set themselves apart organisationally, while the management dedicates its efforts to the integration of its functional forces. However, the bottleneck in most inventory control procedures is data inputs and their utilisation.
Many inventory management decisions have been reduced to formulae, some of which are very simple. Whenever some decisions can be reduced to routine operations, the human mind is freed from tedious, repetitive routines and concentrates on more important decision-making, including the determination of optimum routines and a well-balanced set of objectives.
The statistical tools enable the inventory manager to exercise better judgement and to capitalise more effectively on his experience. Most inventory principles, problems, decisions and procedures are concerned with the interaction of many variable values – quantities, space, prices, costs and distances.
These variables are related, some according to very definite patterns and others in a loose manner. The interactions of these variables tend to follow mathematical and statistical patterns. They are functionally related.
But mathematics alone, useful and powerful as it is, cannot manage any more than a saw and chisel can make a table. But inventory management and cabinet-making call for human application, not only of appropriate tools but also of judgement and skill.
An understanding of the EOQ principle and the ability to translate that principle into workable operating procedures are necessary for a successful use of the powerful tool of economic lot purchases. Equally important is the control of the tool to meet particular system objectives.
The application of EOQ sometimes fails because the members of an organisation do not grasp the economical and mathematical principles on which it rests or cannot solve the practical problems of data gathering and formula computation.
Very often, the application fails because the inventory manager is dissatisfied with the resulting ordering rates and inventory levels, and is unable to control the operations to achieve satisfactory results.
The success of economic lot purchase requires the inventory manager to:
(i) Set objectives of economic lot purchasing;
(ii) Predict the consequences in terms of ordering rate and inventory levels, of using particular values of order cost and holding rate in the EOQ expression; and
(iii) Select the values that most closely meet stated objectives.